Press releases
From protective suits to specialised trousers: Lüneburg fire service washes with the latest Miele technology
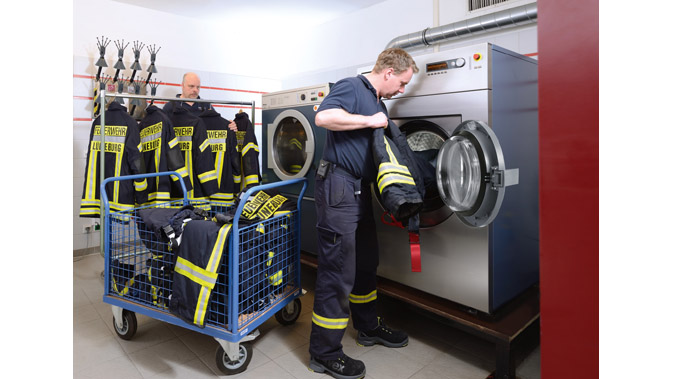
Gentle programmes for textiles containing Aramid and retro-reflective strips
A road accident involving an HGV in pouring rain with sacks of charcoal ripped open and strewn across the road: After this assignment, the protective suits worn by 30 fire-fighters were as black as coal, coated with dust which stuck like pitch. The lads from the Lüneburg brigade in northern Germany can thank their Miele washing machine from the latest model generation that this soil was removed in its entirety. These programmes were developed specifically for fire-fighting apparel involving specialised fabrics to shield against heat and water which need reproofing after washing. These machine have proved their worth over the past two years in practical trials.
'First we were given a prototype and later one of the first pre-series models', says Jörg Förster, full-time equipment manager. Today, these models are available as 'Benchmark' machines, and Förster is now the proud permanent owner of the former test machine. 'I usually wash two and a half suits – three trousers and two jackets, or vice versa'. The drum with a load capacity of 14 kg should not be completely full so as to allow detergents and reproofing agent to unfold their full potential.
Everything used on a day-to-day basis by rescue services comes out clean: Protective suits for fire-fighting, dealing with chemical spillages or diving in the Elbe river, breathing masks and even saftey trousers which prevent injuries when working with chain saws. 'The programmes I use are as different as the textiles we wash', says Förster. 'Retro-reflective strips on protective suits, for instance, do not tolerate high spin speeds. But the water level is higher to enable contaminants to be completely removed with the wash liquor'. Each source of fire with heavy smoke emissions releases carcinogenic substances which settle on fire-fighters' clothing. That is why it is imperative for them to be cleaned thoroughly. According to Förster, a wash cycle followed immediately by reproofing at 40°C takes one hour.
More than 3600 fire-fighters hand in their turnout gear for washing
Sometimes the machine runs the whole day. The 100 or so stations within the area covered by the Lüneburg authority employ more than 3600 voluntary and full-time fire-fighters. Almost all have at some point taken their suits to the main station in Lüneburg for cleaning. Word has spread that protective gear looks as good as new after washing in the patented Miele honeycomb drum. This is also a feature on the same-capacity tumble dryer. Dryers not only activate the reproofing agent applied in the washing machine but also ensure that impermeable, multi-ply composite fabrics with a high proportion of Aramid are thoroughly dried without any damp patches remaining on the inside, thanks to the Air Recycling Plus system.
Miele technology installed in Lüneburg is also used to reprocess breathing masks if there are capacity bottlenecks on the special washer in the neighbouring workshop. Masks are washed in padded protective bags, and for the tumble dryer there are braces, specifically designed by Miele, which provide a secure hold and protect masks from damage in a rotating drum.
'Loading and switching on the two machines is incredibly simple', says equipment manager Förster. Ease of use in operating the washing machine was one of the main reasons for him to buy another Miele when the previous model had come to the end of its useful life. 'The equipment has to be fast when the chips are down – just like we are. We need dependable helpers in the laundry, too, because protective clothing saves lives in an emergency, so we can't afford to cut corners when it comes to looking after our gear'.
(597 words, 3,650 characters incl. spaces)
Company profile: Miele is the world's leading manufacturer of premium domestic appliances including cooking, baking and steam-cooking appliances, refrigeration products, coffee makers, dishwashers and laundry and floor care products. This line-up is augmented by dishwashers, washer-extractors and tumble dryers for commercial use as well as washer-disinfectors and sterilisers for use in medical and laboratory applications (Professional Business Unit). The Miele company, founded in 1899, has eight production plants in Germany as well as one plant each in Austria, the Czech Republic, China and Romania. 2017/18 turnover amounted to approx.
EUR 4.1 bn with sales outside Germany accounting for 70%. Miele is represented with its own sales subsidiaries and via importers in almost 100 countries. The Miele company, now in the fourth generation of family ownership, employs a workforce of around 20,100, 11,200 thereof in Germany. The company headquarters are located in Gütersloh/Westphalia, Germany.
Anke Schläger
+ 49 5241 89-1949
anke.schlaeger@miele.com
Media information
Description | Download |
---|---|
![]() Clean, dry and reproofed: Equipment manager Jörg Förster (rear) and his colleague Michael Voß have their work cut out washing and drying protective suits. |
High Resolution TIFF |
High Resolution JPG | |
![]() Jörg Förster attaches three breathing masks to each brace before the brackets are secured inside the dryer drum. Breathing masks are washed in padded protective bags. |
High Resolution TIFF |
High Resolution JPG | |
![]() Ready for service: The vehicle fleet at the Lüneburg fire station. |
High Resolution TIFF |
High Resolution JPG | |
![]() Full lockers await their users. The only difference is in the garment sizes – otherwise, equal opportunities apply as both men and women wear the same protective suits. |
High Resolution TIFF |
High Resolution JPG | |
![]() Major incident: Fire at a wood yard. The day after an incident like this, the washing machine back at the fire station is usually running from morning until evening. |
High Resolution TIFF |
High Resolution JPG | |
![]() This HGV road accident left the protective suits worn by fire-fighters blackened. The reason for this were the white sacks full of charcoal which had to be unloaded at the double – producing dust which stuck to clothing like pitch in the pouring rain. |
High Resolution TIFF |
High Resolution JPG |